Scalable Superhydrophobic Copper Oxide Surfaces for Enhanced Heat Transfer
- Category: Energy, Materials, Nanotechnology
- Tags: evelyn wang, nenad milijkovic
Vapor condensation is observed in everyday life and routinely utilized in industry as an effective means of transferring heat. In industrial systems, the condensed vapor typically forms a thin liquid film due to the high surface energy associated with the majority of industrial heat exchanger materials (i.e., clean metals and metal oxides). This filmwise condensation mode is not desired due to the large thermal barrier for heat transfer. If the condensing surface is coated with a functional hydrophobic coating, for example a long chain fatty acid or polymer coating, the vapor forms discrete liquid droplets. These droplets shed at sizes approaching the capillary length (≈2 mm for water) and refresh the surface for re-nucleation. Furthermore, when micro- or nanostructures are combined with the coating, a superhydrophobic surface can be created with smaller droplet shedding radii (≈10-100 µm) than dropwise condensation and potential droplet jumping during coalescence due to the conversion of surface energy to kinetic energy (Figure 1a). In this work[1], we experimentally demonstrated that a 25% higher overall heat flux (Figure 2a) and 30% higher condensation heat transfer coefficient (Figure 2b) can be achieved using silanized CuO superhydrophobic surfaces (Figure 1b and c) compared to conventional dropwise condensing Cu surfaces. We show that these CuO surfaces offer ideal condensation behavior in terms of emergent droplet morphology and coalescence dynamics, and a significant enhancement in heat transfer performance. Furthermore, the chemical-oxidation-based CuO fabrication process provides a simple and readily scalable method to create superhydrophobic condensation surfaces that can sustain droplet jumping behavior. Accordingly, these surfaces are attractive for applications such as atmospheric water harvesting and dehumidification.
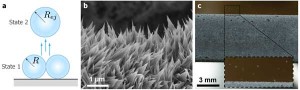
Figure 1: (a) Schematic of the droplet jumping mechanism showing two droplets with radii R, prior to (state 1) and immediately after (state 2) coalescence. (b) Side view field emission scanning electron microscopy FESEM image of a nanostructured CuO surface. The sharp, knife-like CuO structures have characteristic heights, h ≈ 1 μm, solid fraction, φ ≈ 0.023, and roughness factor, r ≈ 10. (c) Jumping-droplet superhydrophobic condensation on a nanostructured CuO tube (Inset: magnified view of the jumping phenomena). The tube sample has outer diameter DOD = 6.35 mm, inner diameter, DID = 3.56 mm, and length L = 131 mm.
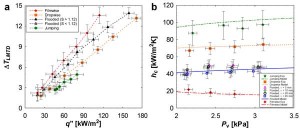
Figure 2: (a) Experimental steady state log mean water to vapor temperature difference (ΔTLMTD) as a function of overall surface heat flux (q”) for tube surfaces undergoing filmwise, dropwise, flooded, and jumping condensation with chamber vapor pressure Pv = 2700 ± 68 Pa. Rapid droplet removal due to coalescence induced droplet jumping results in the highest heat fluxes for the jumping sample (S < 1.12). (b) Experimental and theoretical steady state condensation coefficient (hc) as a function of saturated vapor pressure (Pv) for tube surfaces undergoing filmwise, dropwise, flooded, and jumping condensation. Jumping condensation shows the highest condensation heat transfer coefficient for low supersaturations (S < 1.12).
- N. Miljkovic, R. Enright, Y. Nam, K. Lopez, N. Dou, J. Sack, and E. N. Wang, “Jumping-Droplet-Enhanced Condensation on Scalable Superhydrophobic Nanostructured Surfaces,” Nano Letters, vol. 13, no. 1, 2013, pp. 179-187. [↩]