Sintered Metal Wicks for Loop Heat Pipes
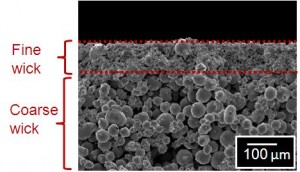
Figure 1: Sample of bi-layer wick. The wick shown consists of a 40-90-µm coarse copper powder in the bulk and a 5-15-µm fine copper powder layered on top.
Loop heat pipes (LHPs) are a widely-used component in the thermal management of high-power electronics. LHPs transfer heat by utilizing the latent heat of a working fluid, which is circulated by the capillary pumping of a porous wick. A typical design consists of an evaporator and condenser connected in a closed loop. As the capillary wick, located in the evaporator, influences the operating characteristics and limits of the LHP, much work has been devoted to optimizing the wick’s capillarity and permeability to extend the range of LHP operation [1] [2] [3].
This work investigates the wick characteristics necessary to operate a novel, multi-condenser LHP. To ensure controlled condensation and full utilization of all condensers, an additional wick must be integrated into the condensers. Condensation occurs on the wick’s surface, and the wick is used to separate the vapor and liquid phases. The wick must therefore have high capillary pressure at the interface to separate the phases and high bulk permeability for ease of liquid flow.
To achieve high capillary pressure at the wick surface and high bulk permeability, a bi-layer sintered wick structure was fabricated in two steps (Figure 1). The bulk wick was first made by sintering coarse (120-140 µm) copper powder at 850 °C for 30 minutes. The sintering was performed in a tube furnace under a hydrogen-nitrogen atmosphere. A thin layer of high-capillarity wick was then fabricated on top of the bulk wick by layering fine (5-15 µm) copper powder and sintering at 650 °C for 30 minutes. A controlled fabrication procedure resulted in a repeatable thickness of the fine layer of approximately 100 µm. The bi-layer wick showed improvement over the single-layer coarse wick, matching the permeability (10-11 m2) of the coarse wick in the bulk while increasing the surface capillary pressure from 100 to 680 Pa for the advancing meniscus.
References
- J. Ku, “Operating characteristics of loop heat pipes,” SAE 1999-01-2007. [↩]
- C.C. Yeh, B.H. Liu, and Y.M. Chen, “A study of loop heat pipes with biporous wicks,” Heat and Mass Transfer, vol. 44, pp. 1537-1547, April 2008. [↩]
- X. Huang and G. Franchi, “Design and fabrication of hybrid bi-modal wick structure for heat pipe application,” Journal of Porous Matter, vol. 15, pp. 635-642, July 2007. [↩]