Porous Ionic-liquid-ion-source Emitter Arrays for Spacecraft Propulsion
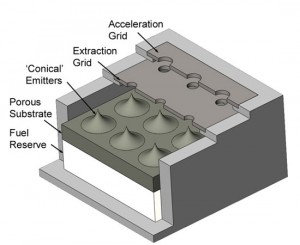
Figure 1: Proposed ILIS thruster using porous emitter substrates. Propellant can be supplied by capillarity from a reserve tank mounted behind the substrate. A two-grid system allows for modulation of both the current and the beam energy.
Ionic Liquid Ion Sources (ILIS) are a subset of electrospray emitters characterized by pure ion emission from room-temperature ionic liquids. Previously these sources have been shown to be a simple and efficient source of both positive and negative ions that could be used, amongst other applications, for spacecraft propulsion [1]. However, the low (<1µN) thrust levels per emitter require practical thrusters to employ arrays of emitters. At modest packing densities, a few tips per square millimeter, the thrust per unit area approaches that of more traditional plasma based ion thrusters [2]. Initial efforts focused on creating arrays of externally wetted emitters from silicon [3]. These studies were plagued by poor and/or inconsistent wetting. As an alternative, we are developing arrays fabricated from bulk porous materials. Here capillarity alone provides passive and consistent wetting of the emission sites. We have observed that this feed mechanism can yield a larger current range than externally wetted emitters while continuing to operate in the purely ionic regime [2]. Using porous emitters, a thruster configuration as in Figure 1 is envisioned.
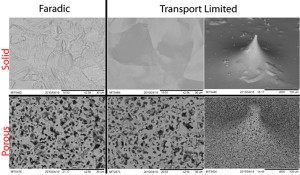
Figure 2: Examples of electrochemical etching both within the Faradic regime, where rough-etching favors crystal planes and can penetrate pores, and in a transport limited regime, where smoother etching of the material surface is achieved.
Fabricating arrays using bulk porous material has resulted in a number of inherent challenges. Electrochemical etching has been a useful tool for fabricating ILIS in the past [1], and our recent findings suggest it may be well suited for etching the surface of a porous material. Specifically, when etching is used with an appropriate tool, a transport limited etch rate can be achieved that promotes smooth, near-isotropic etching of the surface of a porous material with minimal penetration into the pores. Figure 2 demonstrates the results for both porous and solid nickel samples. Additionally, we are beginning to investigate the feasibility of high-pressure molding of powder metals to fabricate the emitters and substrate with molds fabricated using more traditional techniques. To date, basic extraction and acceleration grids have been fabricated from silicon with die-level alignment; however, we plan to move towards a more complete and optimized package within the near future.
References
- P. Lozano and M. Martinez-Sanchez, “Ionic liquid ion sources: characterization of externally wetted emitters,” J. Colloid and Interface Science, vol. 282, pp. 415-421, 2005. [↩] [↩]
- D. Courtney and P. Lozano, “Development of Ionic Liquid Electrospray Thrusters using Porous Emitter Substrates,” 27th International Symposium on Space Technology and Science, Tsukuba, Japan, 2009. [↩] [↩]
- B. Gassend, “A Fully Microfabricated Two-Dimensional Electrospray Array with Applications to Space Propulsion,” PhD thesis, Massachusetts Institute of Technology, Cambridge, 2007. [↩]