Origin and Control of Intrinsic Stresses in Metallic Thin Films for N/MEMS Applications
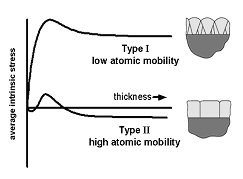
Figure 1: Film stress as a function of thickness. Under conditions of low atomic mobility, non-equiaxed columnar grains and high tensile stresses develop. Under conditions of high atomic mobility, equiaxed columnar grains and tensile or compressive stresses develop.
The mechanical properties of thin films, especially residual stresses in as-deposited films, strongly influence the reliability and performance of microelectromechanical devices and systems. Residual stresses can be as high as 1GPa and can be tensile or compressive, depending on the material, deposition technique, and, very sensitively, deposition conditions. When evaporative deposition is used, the two broad categories of behavior occur (Figure 1). Type I is characterized by development of a high tensile stress that is retained during and after continued deposition. This behavior is common when materials are deposited at low temperatures relative to their melting temperature, e.g. among refractory metals and semiconductors. In Type II behavior, a tensile stress develops as the film first forms, but compressive stresses (as high as 200MPa) develop during continued deposition. This behavior is characteristic of materials with relatively low melting temperatures such as Au, Ag, and Al.
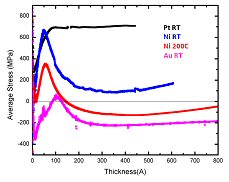
Figure 2: Stress evolution during deposition of Au, Pt, and Ni films at room temperature and a Ni film at 200°C.
The tensile rise seen in both behaviors is thought to arise as islands coalesce to form a film. The origin of post-coalescence compressive stress has been debated extensively over the past decade. Models associated with adatom-surface [1] [2] and adatom-grain boundary [3] interactions have been proposed to explain the compressive-stress generation during deposition and its reversible relaxation during growth interruptions.
We use in-situ stress measurements to follow stress evolution as films are deposited. The measurements can be done with sensitivity to variations associated with sub-monolayer deposition and can be carried out at high sampling frequencies. Through correlation of stress and microstructural evolution, we have shown that reversible stress relaxations that occur during interruptions of growth of Au films vary with the grain size, in general agreement with the model given in reference [3] [4]. However, we also find that the temperature dependence of the reversible stress change is too weak to be consistent with any proposed models. To further characterize stress evolution phenomenology, especially with respect to deposition temperature, we have begun studies of a range of materials. Figure 2 shows results for Ni films deposited at room temperature and 200C. Two observations are noteworthy: the observed behavior is intermediate to Type I and II, and the behavior depends strongly on the deposition temperature. Those results show that the processes leading to the development of compressive stresses are temperature-dependent, even if the process involved in reversible stress relaxations is not.
Through these and other studies, we aim for a comprehensive understanding of factors that affect the residual stress in thin films, so that this stress can be better controlled.
References
- F. Spaepen,“Interfaces and Stresses in Thin Films,” Acta. Materialia, vol. 48, 31 (2000). [↩]
- C. Friesen and C.V. Thompson, “Reversible Stress Relaxation During Precoalescence Interruptions of Volmer-Weber Thin Film Growth,” Physical Review Letters, vol. 89, 126103 (2002). [↩]
- E. Chason, B.W. Sheldon, L.B. Freund, J.A. Floro, and S.J. Hearne, “Origin of Compressive Residual Stress in Polycrystalline Thin Films,” Physical Review Letters, vol. 88, 156103 (2002). [↩] [↩]
- J. Leib, R. Monig, C.V. Thompson, “Direct Evidence for Effects of Grain Structure on Reversible Compressive Deposition Stresses in Polycrystalline Gold Films,” Physical Review Letters vol. 102, 25601 (2009). [↩]