Microfabricated Devices for Portable Power-generation
The development of portable power-generation systems remains an important goal, with applications ranging from the automobile industry to the portable electronics industry. The focus of this work is to develop microreaction technology that converts the chemical energy stored in fuels– such as light hydrocarbons and their alcohols— directly into electricity or into a different energy vector such as hydrogen. Developing devices with high energy-conversion efficiency requires addressing difficulties in high-temperature operation: specifically, thermal management, material integration, and improved packaging techniques.
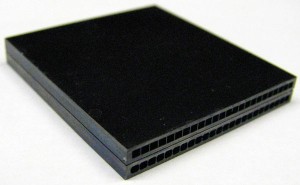
Figure 1: Catalytic combustion device prior to connection to gas distribution manifold. Each of the 48 channels is 1 mm by 1 mm by 31 mm and is separated by a 100-μm–thick wall.
We have developed a catalytic combustion-based device intended for the direct conversion of thermal energy to electricity. The combustor has been designed to achieve attractive energy and power densities while addressing system challenges such as mechanically robust fluidic connections and minimal parasitic power losses related to pressurization of air. The channels of the combustor are etched using wet potassium hydroxide, which is the most economical etch technique available. Straight channels (1mm by 1mm in cross-section) are arranged in parallel and separated by 100-μm –thick silicon walls, in order to achieve low pressure drop (< 300 Pa at 10 SLPM gas flow) with significant surface area (~1 cm2 per channel) for catalyst deposition. Two identical reactors are stacked to increase reactor volume without a significant increase in exposed surface area. External gas distribution manifolds are compression-sealed to the reactor, eliminating the need for glass brazing of tubes, increasing the mechanical robustness of the device, and avoiding large pressure losses associated with flow constrictions. Platinum-on-alumina catalyst has been washcoated on the channel surfaces for the catalytic combustion of butane with air.
The catalytic combustor has been shown to transfer up to 360 W of heat through surfaces intended for thermoelectric power generation, at a maximum surface temperature of 465°C and a thermal transfer efficiency in the range of 73 – 78% (based on fuel lower heating value). The experiments have been performed using conductive heat sinks designed to have a thermal resistance similar to that of a thermoelectric module. As designed, the reactor could also be used for heat integration of multiple reactions, such as catalytic combustion and steam reforming of alcohol for hydrogen production.