MEMS Steam Generators for Ejector Pumps
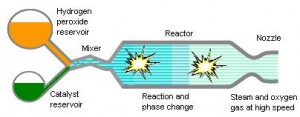
Figure 1: Schematic diagram of a hydrogen-peroxide-based MEMS steam generator, showing the mixer, reactor, and nozzle.
Microscale ejector pumps offer the potential for high-flow-rate pumping of gases, a functionality that is greatly needed in MEMS technology [1]. These pumps have many additional characteristics, such as their simplicity of design and their lack of moving parts, which favor them over other MEMS gas pumps. One of the challenges associated with driving ejector pumps, however, is providing a compact source of motive fluid. This fluid is the high-speed gas that drives the pumping action. The current work delivers a MEMS device capable of generating steam at speeds suitable for driving an ejector pump in a compact fashion. To that end, the device utilizes the homogeneous catalytic decomposition of hydrogen peroxide. Analysis shows that a MEMS ejector pump driven by this device is capable of achieving mass flow rates per unit pump volume on the order of 10-2 g/s/cm3, which is two orders of magnitude higher than the rates of state-of-the-art MEMS gas pumps. In addition to pumping, the steam generator may also be used for microrocket thrust generation in micropropulsion applications.
This work involves the design, fabrication, and testing of the MEMS steam generator. To our knowledge, this device is the first of its kind in the literature that works successfully, and it achieves results that have been sought by other groups for over a decade. The device consists of a mixing section for the peroxide and catalyst streams, a reactor section where the peroxide decomposes, and finally a nozzle section where the gaseous products of the decomposition are accelerated to the required velocities. A schematic is shown in Figure 1. To design the device, multidomain (chemical, thermal, and fluidic) numerically-implemented modeling is used to study the underlying physics and arrive at an optimized, microfabricatable design. The modeling takes into account the key challenges of thermal management, achieving fast mixing [2], and boundary layer compensation. The device is then fabricated from a stack of four silicon wafers and one Pyrex wafer using deep-reactive-ion etching and wafer bonding. A photograph of a microfabricated device is shown in Figure 2. The modeling also guides the design of a mica-based ceramic package which provides both thermal insulation and piping ports. The system is then experimentally tested using 90% high-test hydrogen peroxide and ferrous chloride tetrahydrate solution as the catalyst. The device is characterized using temperature measurements, refractive index analysis, and visual inspection during operation. Successful performance is demonstrated via the full decomposition of the peroxide and the complete vaporization of the water produced. The experimental results are also compared with those from the simulation. Good agreement is observed between experiment and theory, providing comprehensive model verification.
References