Magnetically-assisted Assembly, Alignment, and Orientation of Micro-scale Components
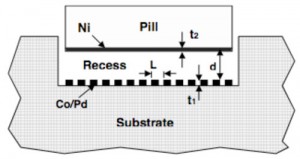
Figure 1: A cross-sectional cartoon illustrating the application of magnetically assisted assembly to recess integration. The variables indicated in the drawing correspond to the model used to calculate the magnetic force intensity.
The use of magnetic forces to improve fluidic self-assembly of micro-components has been investigated using Maxwell 3D to model the forces between Ni thin films on semiconductor device micro-pills and Sm-Co thin films patterned on target substrates [1]. Orienting and restraining forces on pills far in excess of gravity are predicted, and it is found that the fall-off of these forces with pill-to-substrate separation can be engineered through the proper design of the Sm-Co patterns to retain only properly oriented pills [1] [2].
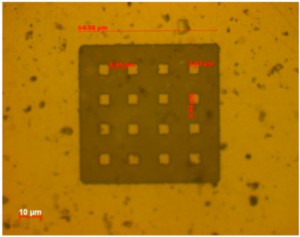
Figure 2: A microphotograph of a patterned samarium cobalt magnetic thin film. The abilities first to sputter-deposit and second to wet-etch thin films like this is critical to the successful implementation of magnetic self-assembly and are unique strengths of the MIT/Queens College effort.
Micro-scale hybrid assembly is a potentially important way of doing heterogeneous integration, i.e., of integrating new materials on silicon integrated circuits to obtain functionality not readily available from silicon device structures alone, and fluidic self-assembly is an attractive way to automate micro-scale assembly. A serious limitation of fluidic self-assembly, however, is the lack of a good method for holding properly assembled components in place and accurately positioned until all of the components have been assembled and they have been permanently bonded in place. We have shown, based on our modeling, that suitably patterned magnetic films can be used to provide the forces necessary to retain, and to accurately orient and position, assembled micro-components.
Our motivation for pursuing micro-scale hybrid assembly is our general interest in doing optoelectronic integration, specifically of vertical cavity surface emitting lasers (VCSELS), edge-emitting lasers (EELs), and light emitting diodes (LEDs), with state-of-the-art, commercially processed Si-CMOS integrated circuits. Our ongoing research integrating these devices on silicon described elsewhere in this report provides the context for this work and illustrates the types of applications we envision for magnetically assisted self-assembly using the results of this study.
Assembly experiments to verify and demonstrate the theoretical predictions are currently in progress using two sizes of 6-µm-thick pills (50 µm by 50 µm and 50 µm by 100 µm) and a variety of magnetic thin film patterns. Recesses with different dimensions are also being studied. [2]
References
- D. Cheng, “Theoretical and Experimental Study of Magnetically Assisted Fluidic Self Assembly,” M.Eng. Thesis, Department of Electrical Engineering and Computer Science, MIT, June 2008. [↩] [↩]
- D. Cheng, J.J. Rumpler, J.M. Perkins, M. Zahn, C.G. Fonstad, E.S. Cramer, R.W. Zuneska, and F.J. Cadieu, “Use of Patterned Magnetic Films to Retain and Orient Micro-Components during Fluidic Assembly,” Journal of Applied Physics, Vol. 105, 07C123, 2009. [↩] [↩]