CNT-enabled Field-ionization Arrays for Portable Vacuum Sources
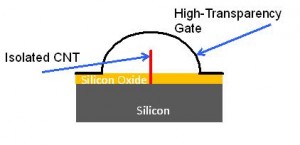
Figure 1: A proposed design of a field-ionizer unit consisting of an isolated vertical CNT and a high-transparency gate with electric field created between them.
Micro vacuum-pump technology, which refers to vacuum-pump systems with miniaturized functional parts, currently attracts a noticeable interest from researchers due to the potential cost savings and energy consumption reduction that they would introduce [1] [2] [3] [4], which would enable portability of many devices that require less-than-atmospheric pressure to operate. In this project we propose a MEMS/NEMS field-ionization micropump that is able to operate at pressures as high as 30 torr and evacuate small (1 mm3) volumes to reach an mtorr-level vacuum. The field-ionization micropump can be integrated with other MEMS/NEMS subsystems to span a pressure range between atmospheric pressure and high vacuum (10-6 torr) to satisfy a wide range of applications that require portable vacuum sources. The field-ionization pump employs arrays of isolated vertically aligned carbon nanotubes (VA-CNTs) that have a proximal gate to generate local high-electric fields (108 V/cm) with low voltage, continuously ionizing gas molecules by field ionization. Positive gas ions then are attracted and implanted into the cathode getter, which is typically biased at 1kV.
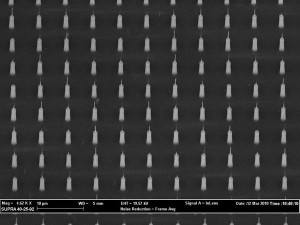
Figure 2: Vertical CNT arrays on silicon columns with 5-um pitch. Catalyst nanodots used for isolated CNT synthesis were defined by the photolithography method.
Our field-ionization pump consists of three major parts: an anode field-ionization array (i.e, the field ionizer), a cathode getter, and a gas inlet/outlet. The schematic diagram of the field-ionizer unit is shown in Figure 1. The fabrication of the field-ionization pump involves the synthesis of isolated VA-CNT arrays at the wafer level. Instead of using low-throughput methods such as e-beam lithography to define the catalyst pads for VA-CNT growth, we have developed a technique that uses projection photo-lithography, which increases the fabrication throughput by four orders of magnitude. Figure 2 is a high-resolution SEM picture of an array of isolated VA-CNTs defined by the projection photo-lithography technique. Simulations of the pump predict an ultra fast air-extracting rate (3 seconds) for a 56-mm3 volume from ionization arrays consisting of 1 million isolated VA-CNTs, while the pump consumes less than 1W. [5]
References
- N. Nguyen, X. Huang, and t. Chuan, “MEMS-Micropumps: A Review,” ASME J. Fluids Eng., vol. 124, pp. 384–392, 2002. [↩]
- P. Woias, “Micropumps—Summarizing the First Two Decades,” Proc. SPIE, vol. 4560, pp. 39–52, 2001. [↩]
- D. Laser and J. Santiago, “A Review of Micropumps,” J. Micromech. Microeng., vol. 14, pp. R35–R64, 2004. [↩]
- S. Shoji and M. Esahi, “Micro Flow Devices,” IEEE Fifth International Symposium on Micro Machine and Human Science, pp. 89–95, 1994. [↩]
- J. Hauschild, E. Wapelhorst, and J. Mueller, “A Fully Integrated Plasma Electron Source for Micro Mass Spectrometers,” in Ninth International Conference on Miniaturized Systems for Chemistry and Life Sciences, pp. 476–478, 2005. [↩]