A MEMS Singlet Oxygen Generator for Powering Chemical Lasers
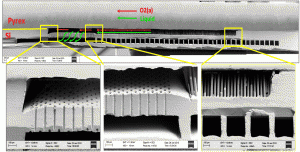
Figure 1: Cross-sectional scanning electron micrograph of the singlet-oxygen generator. The generator is formed from a stack of two silicon wafers and one Pyrex wafer. Right inset: microstructured reaction channels (above) and heat exchanger channels (below). Center inset: reaction-channel exit and leading edge of the capillary-separation region for separating gas phase and liquid products. Left inset: End of capillary-separation region.
Singlet delta oxygen (O2(a)) may be synthesized through the highly exothermic multiphase reaction of gaseous Cl2 with an aqueous mixture of concentrated H2O2 and KOH. Among other applications, O2(a) may be used to drive a chemical oxygen iodine laser. The laser application of O2(a) generation requires a high yield (i.e., a high fraction of product oxygen in the O2(a) state) and conversion of Cl2 to O2(a) to sustain laser emission; the high yield is achieved in part by effective mixing of the gas and liquid reagents. Modeling suggests that the MEMS singlet-oxygen generator (SOG) has key advantages as compared with fully macroscale implementations [1]. These advantages include smaller hardware size for the same power level, higher yield, more efficient reactant utilization, gravity independence, and feasible batch manufacturing.
Previously, the MIT microSOG team has demonstrated working microSOG devices [2] [3]. These devices produced O2(a) with yields of up to 78% and O2(a) flows per unit volume of up to 0.067mol/s/L; this yield was a significant improvement and the flows per unit volume were comparable to macroscale counterparts. Building on recent successes in this area of innovation [2] [3], we are creating new microSOG chips to improve the Cl2 utilization and O2(a) flow rate by optimizing the mixing, flow distribution systems, and device packaging. Mixing is promoted by an array of microstructured posts that fill the reaction channels; the size of these posts is reduced as compared with earlier systems to enable more compact microSOG chips and a higher contact area per unit volume, which enables high Cl2 utilization (more than 95%) and O2(a) yield (more than 70%). The new device is predicted to operate at a maximum O2(a) flow rate of 1000sccm, for a 7x increase in output flow per unit volume from 0.067mol/L/s [3] to 0.50 mol/L/s. The chip was fabricated from a stack of two silicon wafers and one Pyrex wafer using bulk micromachining (primarily DRIE and bonding technology). An SEM image of the generator and the finished chip are shown in Figures 1 and 2, respectively. Testing is underway.
References
- B.A. Wilhite et al., “Design of a MEMS-based microchemical oxygen–iodine laser (μCOIL) system,” IEEE J. Quantum Electron., vol. 40, no. 8, pp. 1041–1055, Aug. 2004. [↩]
- L.F. Velasquez-Garcia, T.F. Hill, B.A. Wilhite, K.F. Jensen, A.H. Epstein, and C. Livermore, “A MEMS singlet oxygen generator-part I: Device fabrication and proof of concept demonstration,” IEEE Journal of Microelectromechanical Systems, vol. 16, no. 6. pp.1482-1491, 2007. [↩] [↩]
- T.F. Hill, L.F. Velasquez-Garcia, B.A. Wilhite, W.T. Rawlins, S. Lee, S.J. Davis, K.F. Jensen, A.H. Epstein, and C. Livermore, “A MEMS singlet oxygen generator-part II: Experimental exploration of the performance space,” IEEE Journal of Microelectromechanical Systems, vol. 16, no. 6, pp.1492-1505, 2007. [↩] [↩]